Laser cutting of the highest order!
Flow drilling is a non-cutting method of drilling holes in metal. The flow drill is pressed against the workpiece with high pressure, which generates a lot of frictional heat. This changes the material into a plastic, liquid form. The flow drill goes through the material and makes a hole in the workpiece. The excess material forms a bushing around the hole.
The process of flow drilling
Flow drilling involves pressing a carbide-tipped pointed object against the material with extremely high circular movements. The frictional heat released in the process pushes the so-called flow drill through the material, creating a hole and bushing that has a maximum of three times the wall thickness of the material. The space can be used to roll threads through.
Advantages of flow drilling
- Extremely efficient and very fast process
- Production process offers the opportunity to tap threads even in (very) thin material
- No waste is created because no machining takes place
- Less play due to high quality of thread
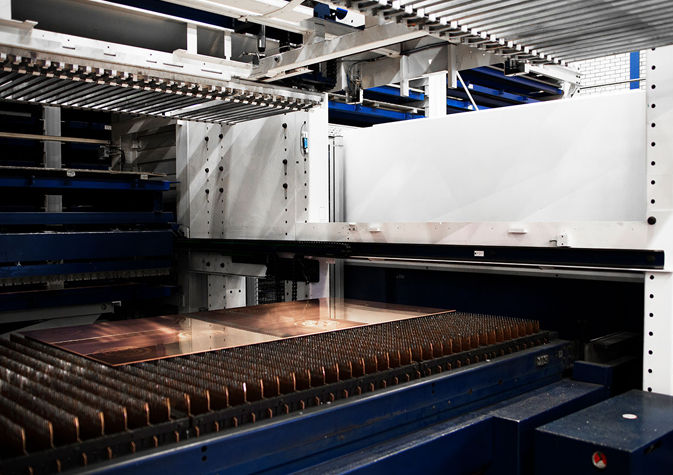
Possible applications
Flow drilling can be used to apply threads to thin materials where tapping is not possible. Baas Metaal BV uses the production process for products made of steel, aluminum, copper, brass, and stainless steel, among other things.