Laser cutting of the highest order!
Many Baas Metaal customers choose pressing as a more attractive option than welding nuts and bolts. Fastening material is applied fully automatically to the thinnest sheet materials, which are also finished waterproof. After pressing, the number of follow-up treatments decreases on average, such as during subsequent coupling, which leads to cost savings.
Fast and precise pressing
Our pressing machine applies fully automatic, fast and accurate mounting materials, such as bolts and nuts, into thin sheet material. Baas Metaal BV has a Pemserter pressing machine, which can be adjusted using a touchscreen. A Servo press system lowers the punch, with the bolt or nut attached to it, at high speed. There you can check whether the mounting material has been applied correctly, after which it can be installed. The pressing machine itself determines the required pressing time, which means that Baas Metaal BV can also press stainless steel plates.
Pressing is cost-saving
Press-in nuts can be very cost-saving during design. Many of our clients often overlook the fasteners during the production and assembly process, partly because the fasteners only make up a small part of the total price of a product. One of the advantages of press-in nuts is that the parts can apply threaded elements at high speed. A standard press can easily place the fasteners into drilled, lasered or punched holes.
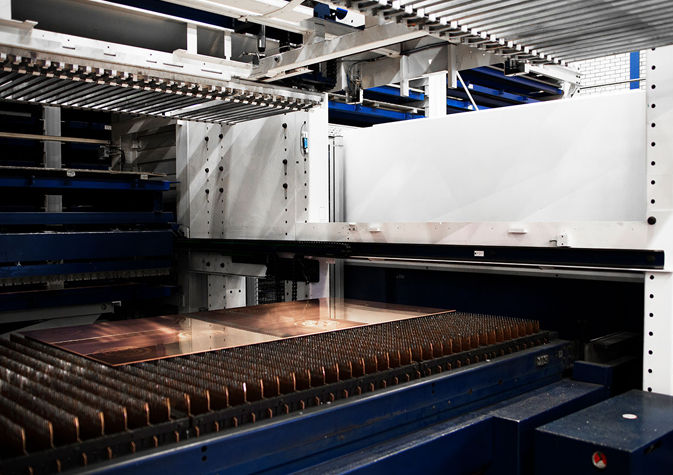
Press-in nuts versus weld nuts
- Parts can be positioned extremely precisely in drilled, lasered or punched holes
- Product remains clean: there are no welding fumes or spatters, so wet tapping is not necessary.
- Surface remains undamaged
- No pre-treatment required (degreasing, deburring, etc.)
- The plate is not heated
- Strong connection with sufficient threads and strength classes of your choice